Skip to main content
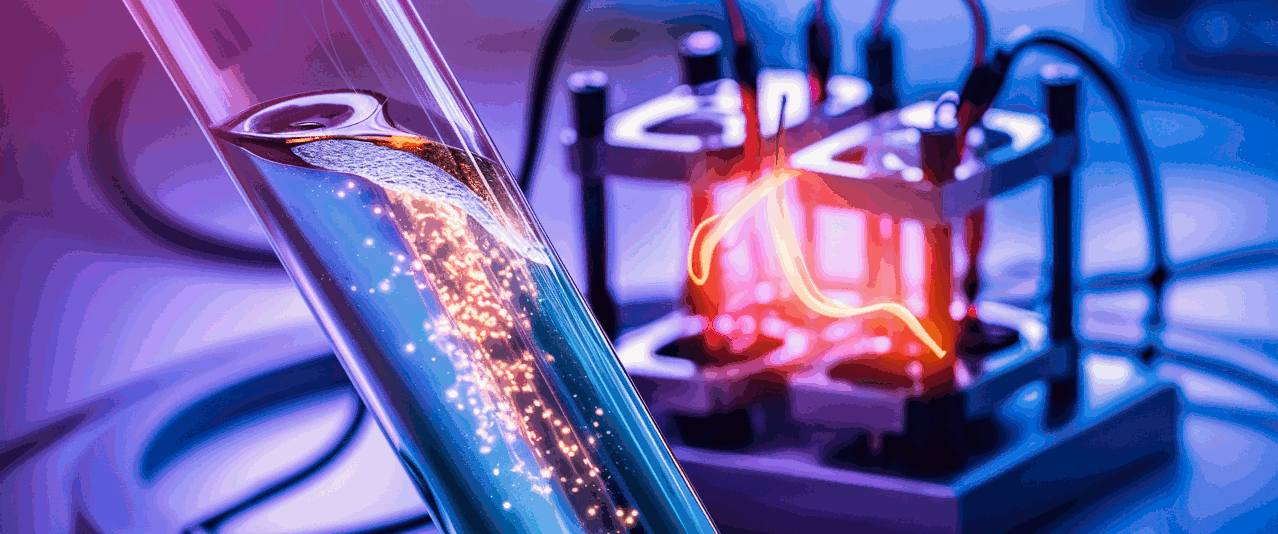
Resonance Frequency Technology (RFT) Innovation in Electrochemical Sector
Over the course of a decade, the BLULAB team has streamlined and perfected the electrolysis process through the development of a series of novel electrochemical reactors that allow for the splitting of water molecules to obtain hydrogen and oxygen in gaseous form using only demineralized water and low-voltage electric current, without employing any type of chemical electrolyte. At the heart of these processes lies Resonance Frequency Technology (RFT). The resonance frequency of a system is the frequency at which the system responds with the maximum amplitude of oscillation. In other words, it is the frequency at which an oscillating system resonates or vibrates most efficiently.
This methodology, based on the principles of water coherence and the use of nearly free electrons, represents a significant advancement in energy storage and pollution reduction.
BLULAB's resonance electrolysis exploits the cohesive properties of water to optimize the process of separating the elements that constitute water, allowing for greater efficiency and reduced energy input. The use of highly mobile electrons within our systems enables faster and more controlled reactions.
The principle of resonance is based on the interaction between a periodic external force and an oscillating system. When the frequency of the external force coincides with the natural frequency of the system, resonance occurs. During resonance, the energy transferred to the oscillating system is maximum, leading to a significant increase in the amplitude of oscillations.
R.F.T. technology applied in electrolysis is a process that involves modulating the frequency and amplitude of the square wave of electrical input to the reactor, where electrolysis takes place. The modulation, driven by a specific algorithm, is defined based on the instantaneous operating conditions of the electrolytic reactor and the demand for gas production, optimizing current absorption to achieve maximum energy efficiency.
After perfecting RFT technology, the engineering team at BLULAB developed a series of electrolytic reactors complete with control electronics, dedicated to the production of hydrogen and oxygen in gaseous form for the terrestrial transport sector, maritime transport, and heating. The goal achieved by the BLULAB team was to stabilize, secure, and make reliable the resonance electrolysis technology to produce pure oxyhydrogen on board transport vehicles and for residential heating boilers.
The invention presents significant innovations; it is able to dynamically control the production of combustible gas. The gas is produced in response to pressure on the accelerator pedal, providing "fuel" derived from demineralized water. The implemented algorithms ensure balanced mixtures at both low and high engine speeds, maximizing reactor performance by excluding accumulations of unused gas. In terms of safety, multiple sensors have been introduced which constantly verify predetermined temperature thresholds, both in the electrolytic cells and in the circuit itself, automatically adjusting operating currents based on temperature. A level sensor, when necessary, activates an electro-pump that maintains a constant water level in the reactor.
BLULAB technology is the result of a multitude of studies, research, patents, and production systems that have led to decisive progress in the field of electrolysis, a phenomenon long known. The key points of R.F.T. technology are:
a) the ability to perform the electrolytic process in the absence of chemical additives;
b) the energy efficiency with which it is possible to carry out this process;
c) the speed and responsiveness of the process in producing high quantities of oxyhydrogen in real-time;
d) the ability to achieve a process almost devoid of maintenance.
The use of oxyhydrogen optimizes combustion processes in endothermic engines and reduces consumption. The energy efficiency of BLULAB technology further improves this aspect. Moreover, the quality and characteristics of the gas delivered induce the reduction of pollutants in exhaust fumes of toxic particles emissions and the reduction of engine noise (over 40% less background noise detection).
The electrolytic reactors are controlled by intelligent electronic circuits, equipped with safety sensors, such as circuit temperature and the temperature of the water involved in the electrolytic process. The systems presented here also include water level control and automatic replenishment from a secondary tank, simultaneous regulation of hydrogen and oxygen production is synchronized with engine load via WiFi communication between the reactor and the vehicle's ECU.
The architecture and engineering of Resonance Frequency Technology, applied in operational flows and motion for depression, predispose the maximum safety and reliability of the devices, inhibiting the possibility of explosions and stagnation of flammable gases inside the reactor itself, maintaining total safety in operational processes.
The plants as a whole are equipped with an injection system that, through a micro-compressor, pushes the on-demand produced combustible gas into the engine's intake circuit, simulating a cylinder for storing combustible gas.
Another revolutionary aspect enabled by BLULAB's technology is electromethanation, a process that utilizes pure oxyhydrogen generated through electrolysis and combines it with CO2 emitted from the exhaust gases of internal combustion vehicles or heating boilers in real-time. This synergy allows the conversion of CO2, a harmful greenhouse gas, into synthetic methane (CH4), a cleaner and more renewable fuel among fossil fuels. The electromethanation technology not only contributes to reducing environmental impact by cutting harmful emissions but also seamlessly integrates with existing market technologies that can be retrofitted.
The devices developed by BLULAB are designed following high safety standards and are ready to undergo rigorous certifications. This focus on safety ensures that the proposed technologies are reliable and compliant with industrial regulations.